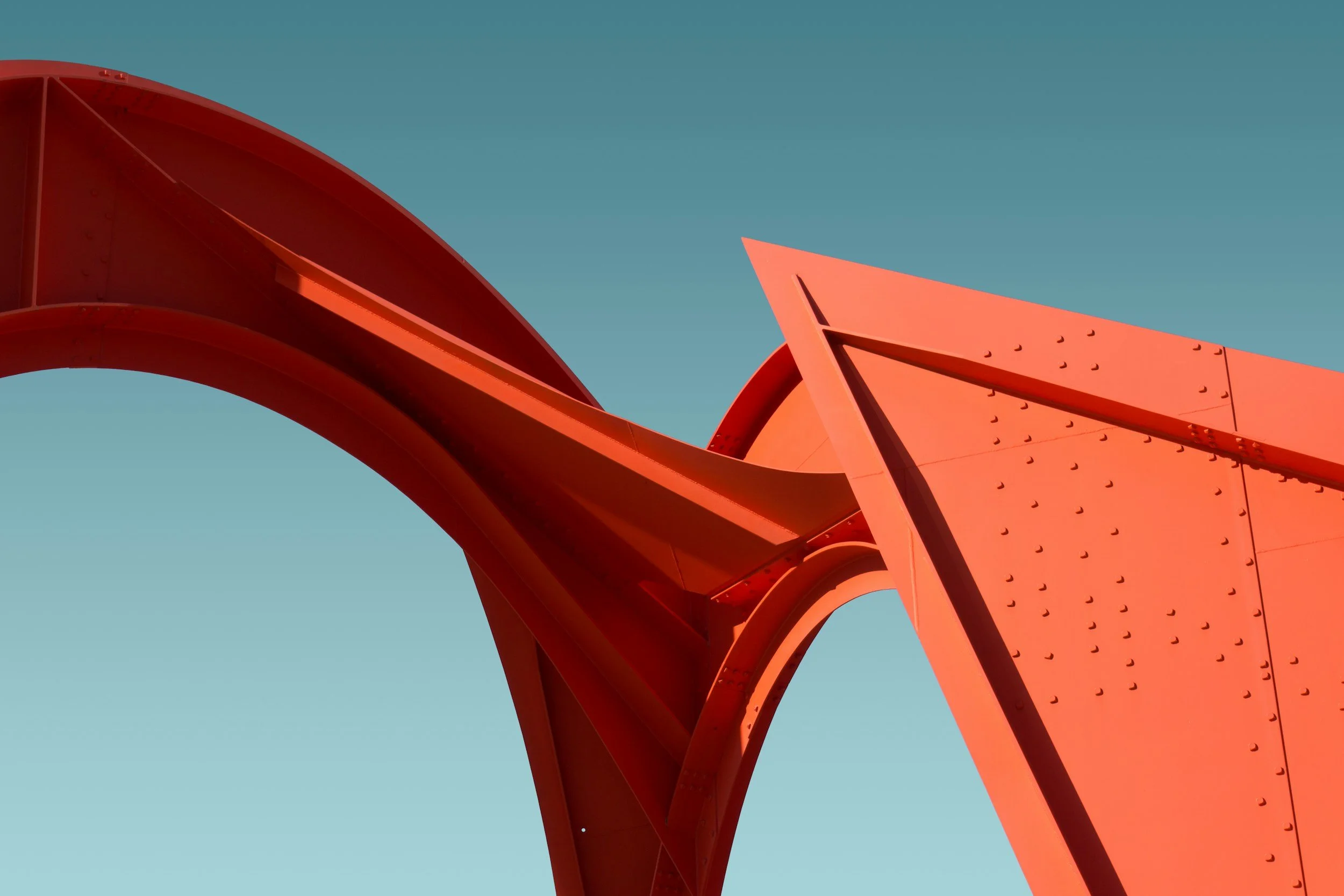
Our In-House Technologies
TIG Welding
(Tungsten Inert Gas Welding)
TIG welding employs a non-consumable tungsten electrode to create the arc. The welder manually feeds a separate filler rod into the weld pool. The process requires a shielding gas, typically pure Argon, to protect the weld area from oxidation.
Precision and Control: TIG welding allows for precise control over the weld, making it ideal for intricate, high-quality welds.
Clean Welds: Produces very clean and visually appealing welds with minimal spatter.
Applications: Best for thinner materials like stainless steel or aluminum. It is often used in aerospace, automotive, and artwork projects.
Stick Welding
(Shielded Metal Arc Welding)
Stick welding uses a consumable electrode coated in flux. As the arc forms between the electrode and the base metal, the flux coating melts, creating a shielding gas and slag to protect the weld from contamination. The slag must be chipped away after the weld cools.
Versatility: Stick welding can be used in a wide range of environments, including outdoor and windy conditions, due to its self-shielding nature.
Durability: It’s effective for thicker and rusted or dirty materials, which makes it popular for repair and maintenance work.
Applications: Commonly used in construction, structural welding, pipelines, and heavy-duty repairs.
MIG Welding
(Metal Inert Gas Welding)
MIG welding uses a machine-fed, consumable wire electrode to create an electric arc between the electrode and the base metal, which melts the wire and forms the weld. An inert gas (such as Argon or a mix with CO₂) flows through the welding gun to protect the weld pool from atmospheric contamination.
Speed and Efficiency: MIG welding is known for its speed and efficiency, making it ideal for projects where high deposition rates are needed.
Applications: Best suited for thicker materials like mild steel, stainless steel, and aluminum. It’s commonly used in automotive repair, manufacturing, and heavy-duty applications.
Gas Welding
(Oxy-Acetylene Welding - OAW)
An oxy-acetylene torch is used to melt the edges of the base metals to be joined. The heat from the torch is sufficient to fuse the edges directly, allowing the metals to bond as they cool and solidify. The weld is formed purely from the melted base metals.
Portability: The welding setup can be relatively portable since it doesn’t rely on an electrical power source.
Applications: Often used in jewelry making, artistic metalwork, and for repairing small parts or thin sheet metals. It's less common for large industrial applications but remains valuable for niche uses.
Resistance Welding
(Electric Resistance Welding)
Resistance welding joins metals using heat from electrical resistance and applied pressure, without needing filler materials or shielding gases. Electrodes placed on each side of the metals conduct high current, creating heat at contact points to melt surfaces and form a weld under pressure.
Speed and Efficiency: Creates strong welds in seconds, ideal for high-volume production.
Milling
Milling is a machining process that uses a rotating multi-point cutting tool to remove material from a workpiece, shaping it into the desired form. It’s highly versatile, allowing for the creation of complex shapes, slots, holes, and precise surface finishes, commonly used in manufacturing parts for machinery and tools.
Turning
Turning is a machining process where a single-point cutting tool removes material from a rotating workpiece, typically on a lathe. This process shapes the outer or inner surfaces of cylindrical parts, producing components like shafts, bolts, and bushings with high accuracy and smooth finishes.
Sand & Glass Blasting
Sand and Glass Blasting are abrasive processes for cleaning or texturing surfaces. Sandblasting uses sand particles for a rougher finish, ideal for removing rust or paint, while glass blasting employs glass beads or crushed glass for a smoother, gentler finish suited for delicate surfaces or matte effects. Both are effective for surface preparation and finishing.
Forging
Forging is a process where metal is shaped by applying compressive forces, typically through hammering, pressing, or rolling. This process can be performed hot or cold, depending on the metal type and desired properties. Forging enhances the material's strength by refining its internal grain structure, making it ideal for creating durable components.
Grinding and Polishing
They are both finishing processes used to improve the surface quality of metals. Grinding removes excess material and smooths rough surfaces using abrasive wheels. Polishing follows grinding, using finer abrasives to achieve a smooth, reflective finish. Together, these processes enhance both the appearance and durability of metal parts.
Bending
Bending with a Metal Bender involves shaping metal by applying controlled force to form precise angles and curves. Using a metal bending machine or press brake, operators can bend sheets, bars, or tubes to specific dimensions without compromising material integrity.
Surface Finishing
We use various techniques to provide an adequate surface finish. Depending on the needs of the project, different methods offer distinct visual effects and levels of durability. We commonly use traditional painting, polishing, brush finishing, powder coating, and passivation.
Metals Used in Our Production
We work with a variety of metals, both ferrous and non-ferrous, including:
Ferrous Metals: carbon steel (standard), stainless steel, corten steel.
Non-Ferrous Metals: aluminum, zinc, copper, and brass.
Carbon Steel
Available in the form of sheets, profiles, pipes, and rolled sections.
It requires anti-corrosion protection such as painting, galvanizing, or oxidizing. It can also be subjected to accelerated rusting (corten steel), which creates a distinctive protective rust layer.
Stainless Steel
The only type of steel resistant to corrosion without additional protection. It comes in various grades, with A2 (corrosion-resistant) and A4 (acid-resistant) being the two most popular choices.
The surface of stainless steel can be finished in different ways depending on aesthetic or functional requirements: it can be ground, polished, brushed, or acid-etched. Through heat treatment, stainless steel can achieve various colors, such as rainbow, cherry, or blue.
Aluminum
One of its main advantages is its light weight, being three times lighter than steel.
Aluminum corrodes slowly and can be protected by anodizing (electrolytic treatment), which can also give it colors like blue, gold, burgundy, black, or green. Aluminum can also be powder-coated, as regular paint may peel over time. It is essential to avoid direct contact between aluminum and stainless steel to prevent accelerated corrosion of aluminum.
Copper
Known for its durability and distinctive color, copper is a heavy metal, approximately 25% heavier than steel.
One of its most remarkable features is its natural patina; as copper ages, it develops a thin layer of copper oxide on its surface, which gives it a dark brown or turquoise-green color. This patina not only adds a unique aesthetic but also serves as a protective layer, shielding the copper from further corrosion.
Brass
An alloy of copper and zinc in varying proportions, most commonly 7:3. It has a golden color when polished.
Like copper, brass tarnishes over time, developing a thin oxide layer that gives it a dark brown or turquoise hue and protects it from further erosion. Brass is often forged or cast to achieve the desired shape.